Experience Quality: Premier Pipeline Welding Inspection Solutions You Can Depend On
Experience Quality: Premier Pipeline Welding Inspection Solutions You Can Depend On
Blog Article
Crucial Pipeline Welding Inspection Tips for Quality Assurance
Just how can one guarantee the high quality of these welds that connect the pipeline areas? By understanding the essential pipe welding examination suggestions, professionals can avert possible risks, lower costly repair work, and maintain the dependability of these crucial infrastructures.
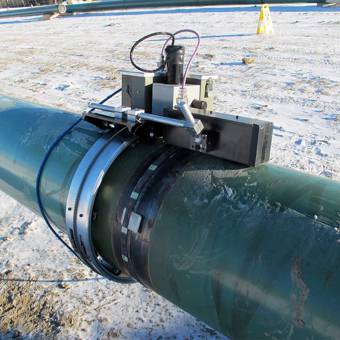
Relevance of Welding Inspection
Welding assessment plays a vital duty in ensuring the structural honesty and safety of pipe systems. By thoroughly examining welds, assessors can recognize any type of flaws or flaws that can compromise the stability of the pipeline. These assessments are essential for protecting against leaks, tears, and other potentially devastating failures that could cause ecological damage, financial losses, and even loss of life.
The importance of welding assessment can not be overstated, as the top quality of welds directly influences the general performance and longevity of the pipeline. Through non-destructive screening approaches such as aesthetic examination, ultrasonic testing, radiography, and magnetic bit screening, assessors can discover defects that might not show up to the naked eye. By recognizing and addressing these issues early, welding assessment aids to ensure that pipelines meet sector standards and regulative demands.
Ultimately, welding evaluation is an important aspect of quality control in pipe fixing, upkeep, and construction (Pipeline Welding Inspection). By upholding strenuous examination requirements, industry professionals can alleviate risks and support the safety and security and reliability of pipe systems
Usual Welding Flaws
Amongst the challenges encountered in pipeline welding, typical issues can significantly impact the architectural stability and performance of the bonded joints. Fractures in the weld can circulate over time, endangering the structural honesty of the pipe. Detecting and dealing with these common flaws with extensive examination and high quality control procedures are important for guaranteeing the reliability and safety and security of pipeline welds.
Inspection Methods for Pipelines


Non-destructive screening (NDT) strategies such as radiographic screening, ultrasonic testing, magnetic bit screening, and liquid penetrant testing are generally made use of in pipe welding inspection. Visual assessment is additionally vital in pipe welding to recognize any visible issues or suspensions. Additionally, automatic evaluation methods utilizing advanced technologies like drones and robotics are progressively being employed to enhance the next page effectiveness and precision of pipeline inspections.
Ensuring Quality Control Standards
To promote strict top quality guarantee requirements in pipe building and construction, meticulous adherence to established industry procedures and standards is crucial. Quality assurance in welding processes calls for a thorough strategy encompassing different stages of pipeline building. Carrying out a durable click here to find out more high quality monitoring system that includes regular audits and evaluations can further improve the overall top quality assurance criteria in pipeline welding.
Preventing Expensive Repairs
Given the crucial importance of maintaining rigid quality control criteria in pipe building and construction, a proactive technique to stop costly repair services is important. By carrying out detailed inspection procedures throughout the welding process, possible concerns can be recognized and remedied at an early stage, eventually saving both money and time. One key element of preventing expensive repair services is guaranteeing that welders are effectively trained and certified, as this significantly decreases the possibility of faulty welds that may cause future failures. In addition, making use of advanced evaluation techniques such as non-destructive testing can help discover any type of issues or inconsistencies in the welds prior to they escalate right into major troubles. Routine upkeep checks and surveillance of environmental elements that could influence the stability of the pipeline are likewise vital Bonuses in avoiding expensive repairs. By buying preventative procedures and focusing on high quality guarantee at every stage of the pipeline welding procedure, companies can decrease the threat of pricey fixings and make sure the long-lasting dependability of their facilities.
Conclusion
To conclude, adherence to appropriate welding examination methods is vital for guaranteeing the high quality and stability of pipelines. By recognizing typical welding defects and carrying out comprehensive inspection processes, pricey repair services can be stopped, and high quality assurance requirements can be met - Pipeline Welding Inspection. It is critical for pipeline welders to focus on inspection procedures to keep the security and integrity of the framework they are working with
The importance of welding inspection can not be overemphasized, as the high quality of welds directly affects the total efficiency and long life of the pipe. Non-destructive screening (NDT) techniques such as radiographic testing, ultrasonic testing, magnetic fragment testing, and fluid penetrant testing are generally utilized in pipe welding evaluation. Visual assessment is likewise essential in pipeline welding to recognize any noticeable issues or interruptions. In addition, automatic assessment methods making use of sophisticated technologies like robotics and drones are increasingly being used to improve the performance and accuracy of pipeline assessments.In final thought, adherence to appropriate welding evaluation strategies is necessary for ensuring the high quality and stability of pipes.
Report this page